Milestones of technology: our iconic reference machines from recent years
Here we present a few reference machines from recent years that combine technical precision and innovation. These include not only new centrifuges but also older models that we have brought up to the latest state of the art, or modifications made for specific customer requirements.
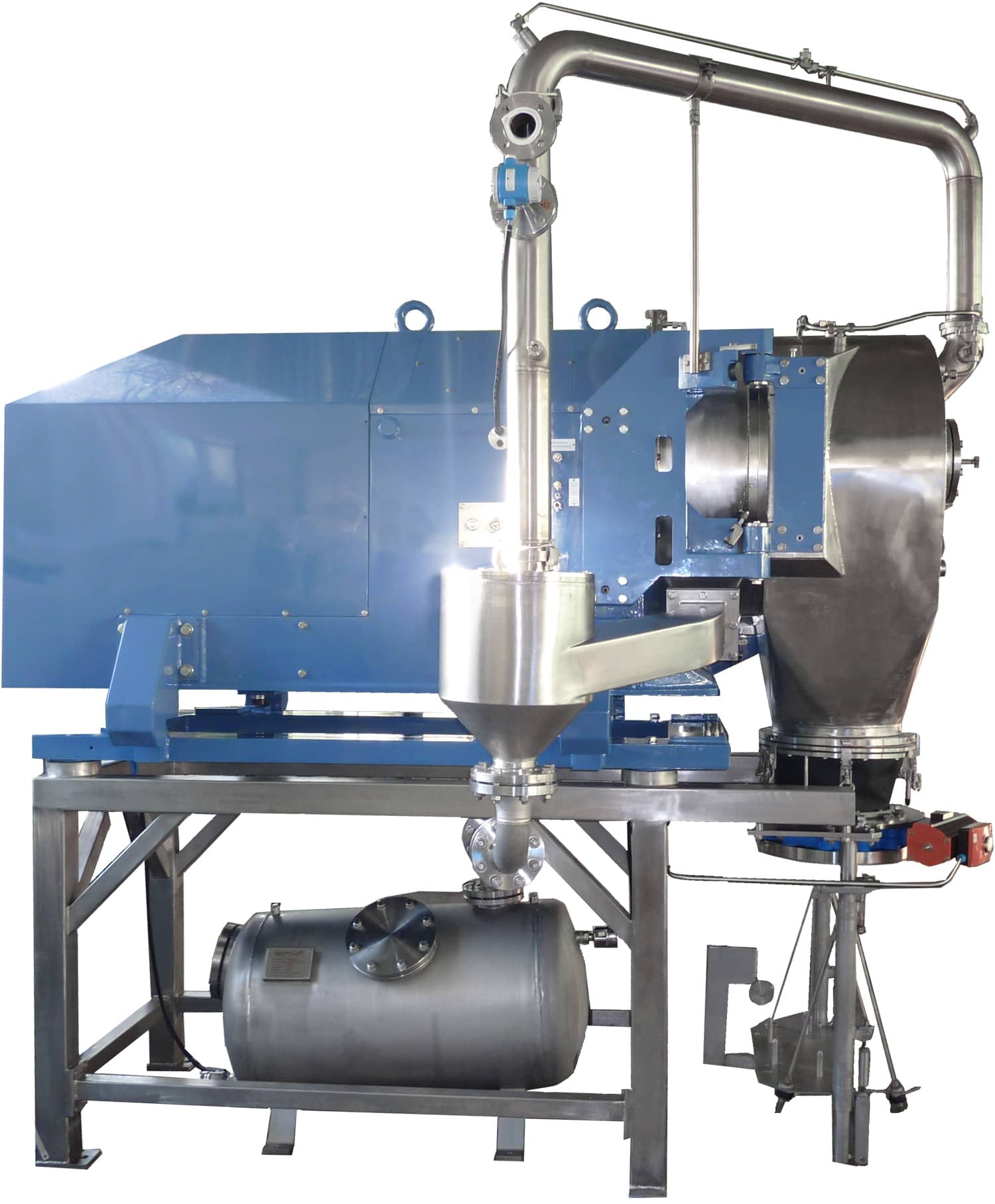
Modernization of a HEINKEL HF600 inverting filter centrifuge.
Modernization of a HEINKEL HF600 inverting filter centrifuge for a Swiss customer. The order includes the ATEX upgrade of the centrifuge, a new safety-oriented control system and inertization unit.
All motors, sensors and valves on the centrifuge were replaced. The connection to the customer's process control system is made via Profibus.
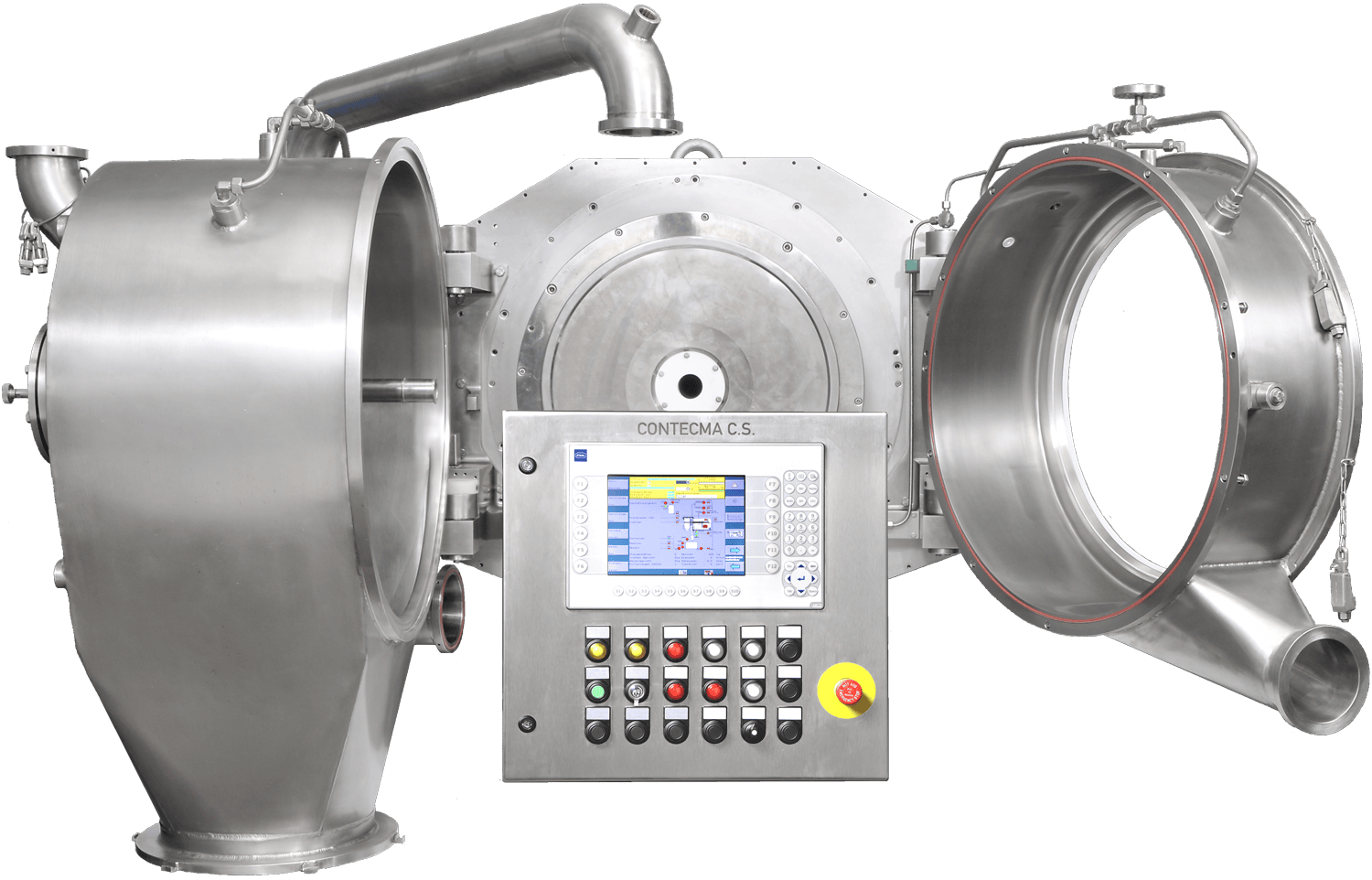
Refurbished HEINKEL HF600.1 inverting filter centrifuge
The centrifuge from the year 1999 was completely disassembled, repainted, and the stainless steel parts re-polished. Additionally, the centrifuge was equipped with the CONTECMA CS patented DFS system.
The DFS system allows the customer to fill the centrifuge under pressure, enabling faster dewatering of the product cake during filling. Naturally, the cake can be overlaid with nitrogen up to a pressure of 6 bar in a further process step. The drum pressure is continuously monitored, and regulated to the customer's preset target value using the valve island developed in-house.
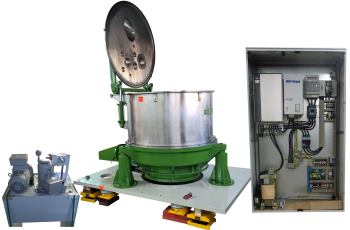
Ellerwerk 736C peeler centrifuge
Ellerwerk 736C peeler centrifuge for our customer in the Bavarian region wanted on the second-hand market.
Naturally repainted in proven CONTECMA CS quality and equipped with a new safety control system. All relevant safety features for EX Zone 1 have been retrofitted. Safety has also been re-evaluated and CE certified in accordance with IEC 61508.

HF800.1 incl. control unit for the USA
We overhauled an inverting filter centrifuge for a US customer in the Chicago area. The US-compliant conversion and the control system were planned and manufactured in-house.
The centrifuge and the HMI are manufactured for EX Zone Class 1 Div 1. A fail-safe CPU from Rockwell takes over the control. The entire documentation was created specifically for the US market.
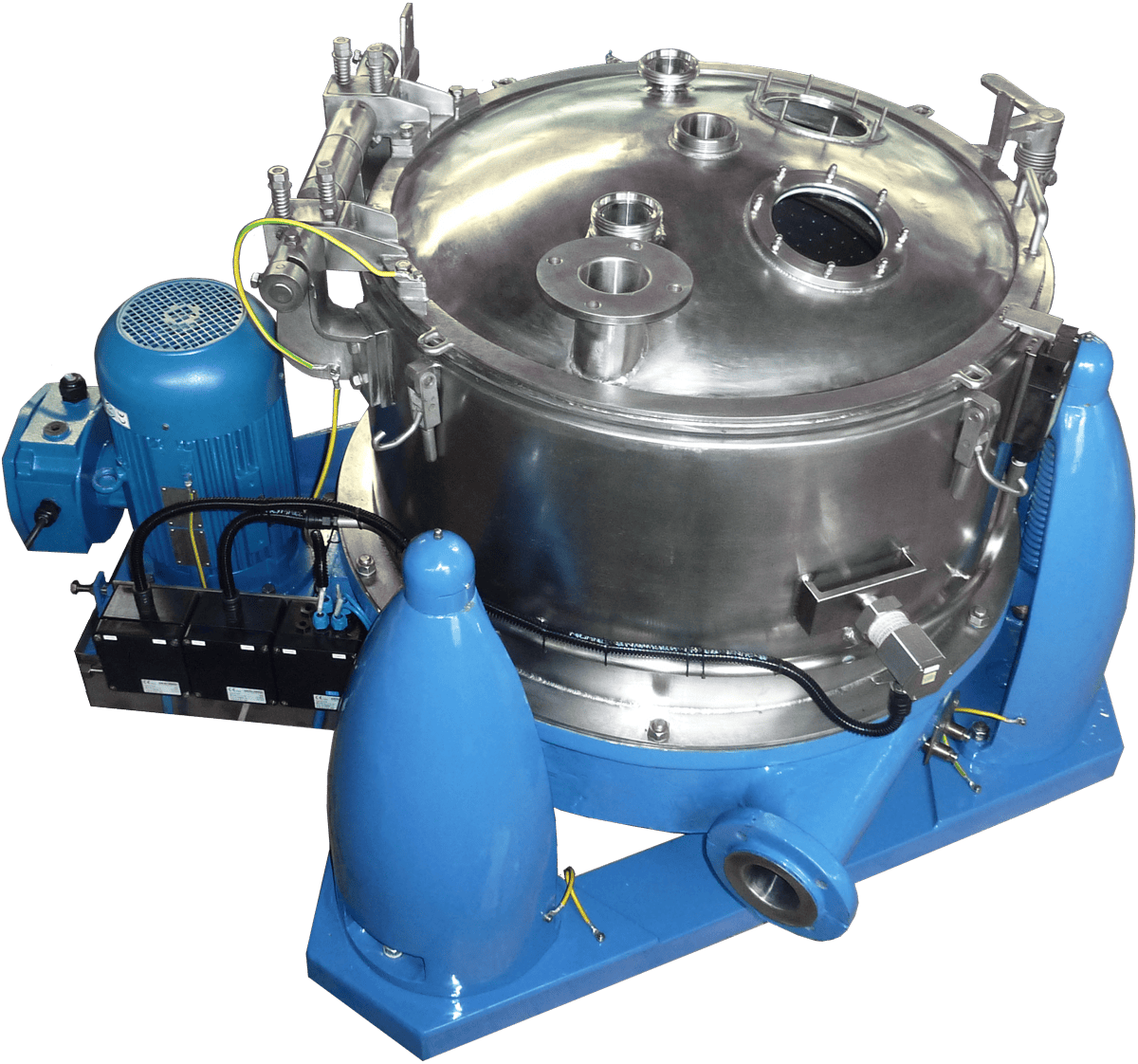
ATEX conversion of a HEINE three-column top discharge centrifuge
At the request of the customer, we modernized the hydraulically driven centrifuge from 1968 to the current state of the art.
For this purpose, the centrifuge was reassessed according to Machinery Directive 2006/42/EC and treated as a new machine. This includes a risk analysis and evaluation of ignition sources of the centrifuge. The insights gained from this were implemented accordingly.
The conversion included the following items
- Conversion of hydraulic drive to electric drive
- Installation of temperature monitoring for bearings
- Installation of N2 inertization
- Installation of housing interlock
- Installation of vibration monitoring
- Installation of speed monitoring
- Replacement of all other electrical components
- New N2 inertization unit with redundant monitoring
- New control unit for Ex ZONE 1
- New safety-oriented plant control
- New painting of the machine body
- UVV compliant with BGR500
- Revision and material testing of all product-contact parts
- Replacement of vibration dampers
- Revision of process connections for inertization, filling, and washing
- Manufacture of new filling line and washing nozzles from HC22
- New system documentation including original operating instructions
- New test book for centrifuges
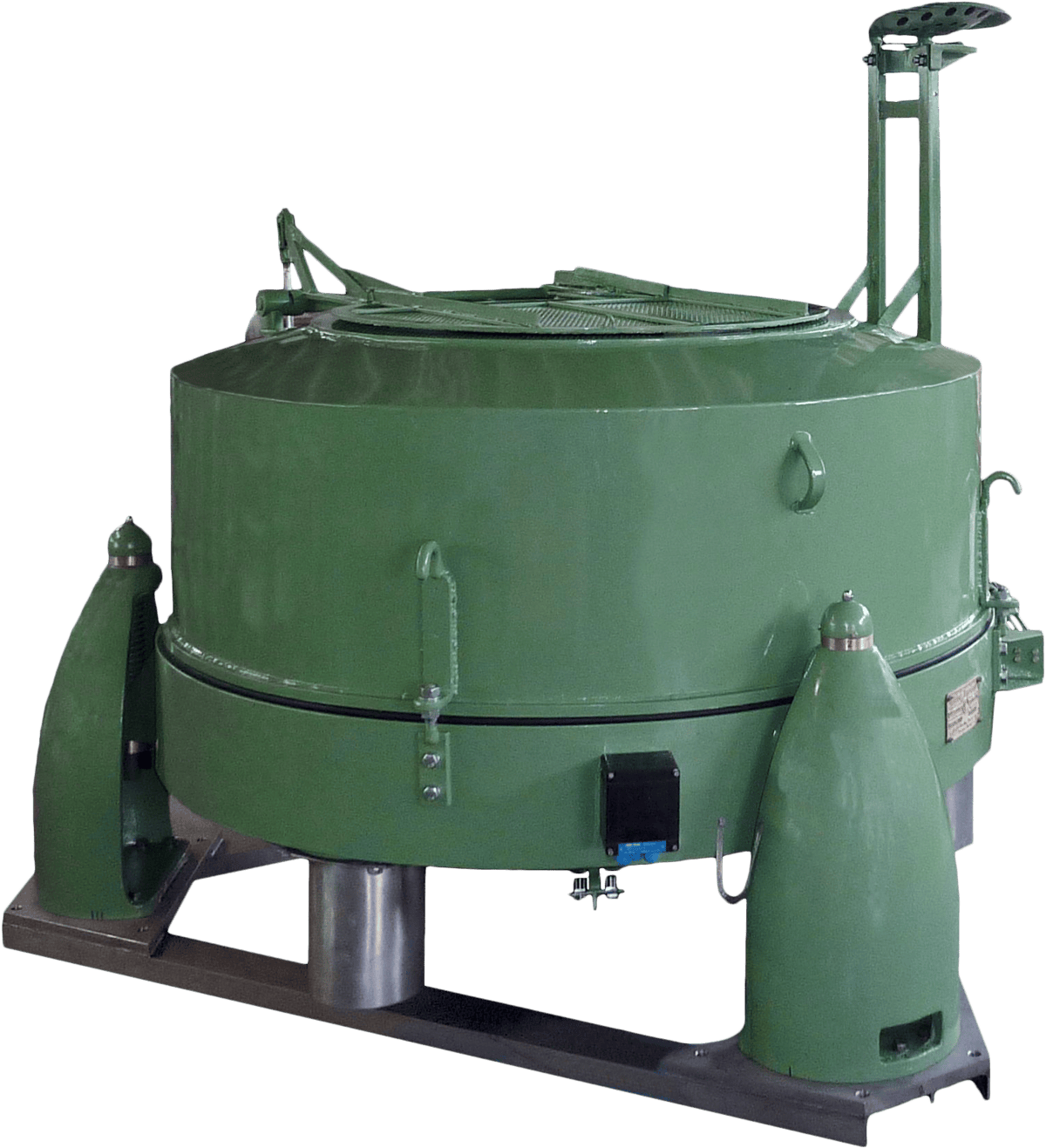
Modernization of a 49-year-old top-discharge centrifuge.
Even a centrifuge from 1965 is not yet obsolete. The directly driven top-discharge centrifuge from HEINE was completely disassembled in our workshop.
All rotating components such as shaft, drum, etc. were inspected for damage and cracks. The bearing seats on the shaft and in the bearing housing were sprayed and reworked. The drive motor was overhauled and high-voltage tested. All components made of mild steel were derusted and repainted.
In terms of safety, the centrifuge was also brought up to date. Added were vibration monitoring, housing monitoring, and speed detection. Thus, a safe and trouble-free operation for the next 50 years is ensured.
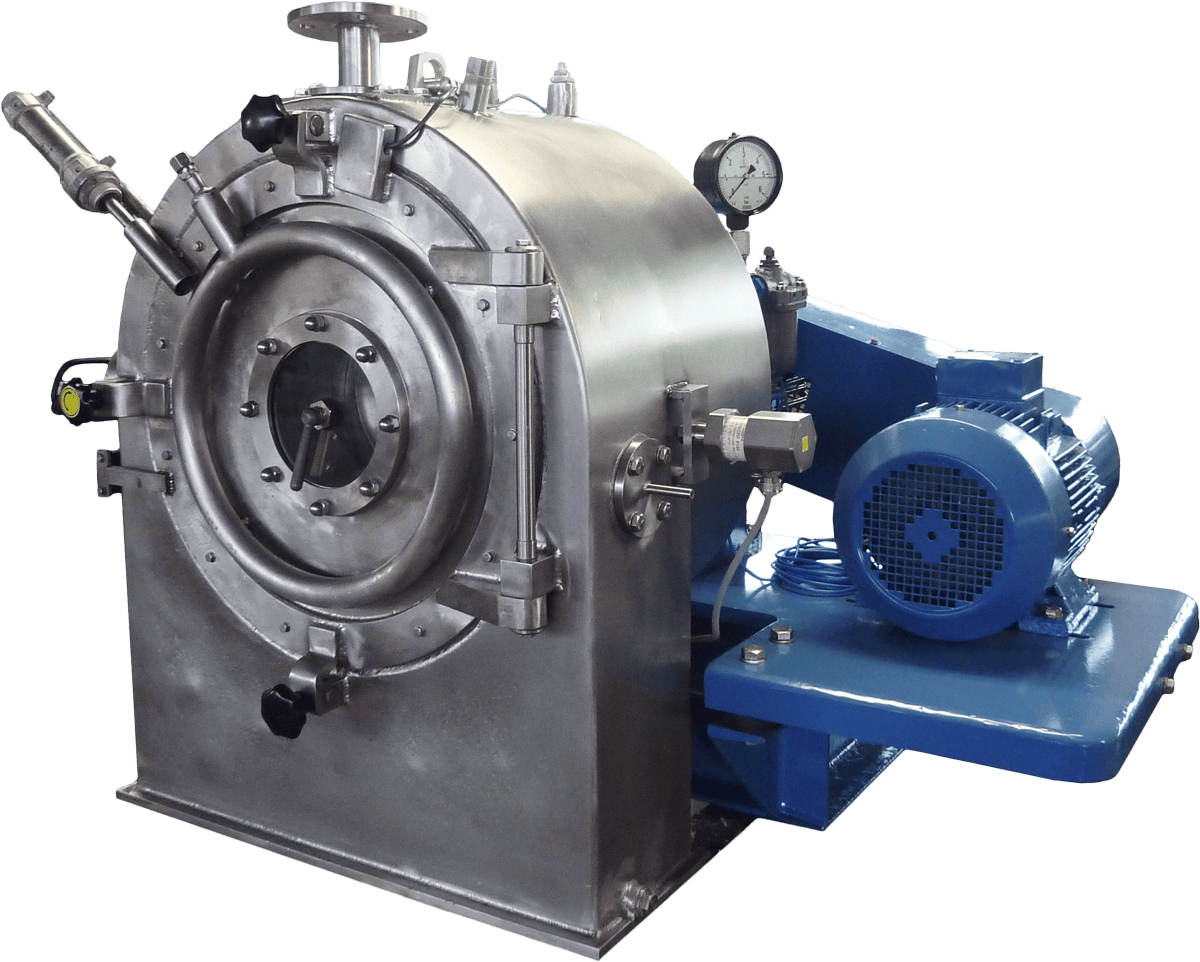
Decanter Centrifuge Modernization.
Modernization of a decanter centrifuge from the manufacturer Siebtechnik for a producer of specialty salts in northern Germany.
The centrifuge was completely disassembled at our facility, all components made of mild steel were repainted, the bearing housing was overhauled, and all seals and vibration dampers were replaced. As part of the modernization, the decanter centrifuge was also brought up to date in terms of safety.
Vibration monitoring, housing monitoring, and speed detection were added. Thus, a safe and trouble-free operation for the coming years is ensured.
Fast and uncomplicated: How to reach us:
Your direct line to us. We are available to answer all your questions about the centrifuge. Our 24/7 technical support hotline is available around the clock. If technical problems arise, our experts are ready to provide immediate assistance. Contact us now for assistance with your challenges.